Glass bottle manufacturing is a highly specialized process that combines art and science to produce containers used across various industries, from beverages to cosmetics. While glass bottles are known for their durability, sustainability, and aesthetic appeal, the manufacturing process is far from straightforward. Manufacturers face numerous challenges in glass bottle manufacturing, ranging from technical issues like defects and inconsistencies to environmental concerns like high energy consumption. In this blog post, we’ll dive deep into the most common hurdles faced by glass bottle manufacturers and explore solutions to overcome these challenges.
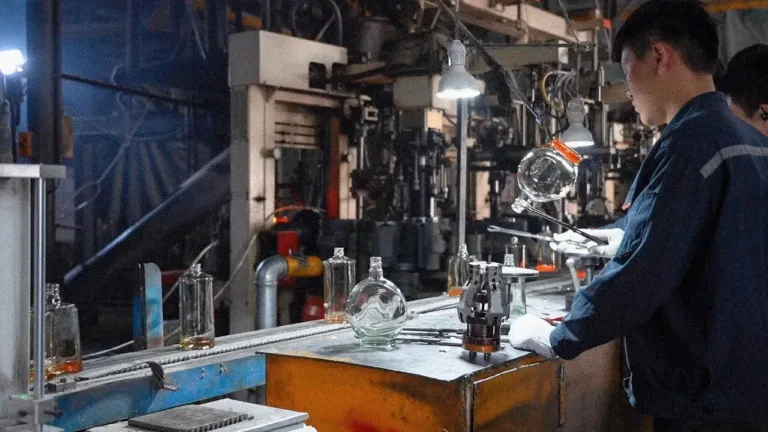
Table of Contents
1. The Glass Bottle Manufacturing Process Overview
How are Glass Bottles Made?
Glass bottle manufacturing begins with raw materials, primarily silica sand, soda ash, and limestone. These materials are combined in precise proportions and heated to temperatures exceeding 1,700°C (3,092°F) to form molten glass. Once the glass reaches its desired consistency, it is shaped into bottles using molds in a process called blow and blow or press and blow. The shaped bottles are then cooled in an annealing lehr, a controlled cooling process that helps relieve internal stresses.
The Role of Technology in Glass Bottle Production
Modern glass bottle production relies heavily on automation to ensure efficiency and consistency. Individual Section (IS) machines are commonly used to form bottles, allowing manufacturers to produce up to 500 bottles per minute. This technology not only improves speed but also reduces the chances of defects by maintaining precise control over the glass forming process. In recent years, manufacturers have also adopted computer-controlled inspection systems to automatically detect defects and ensure quality.
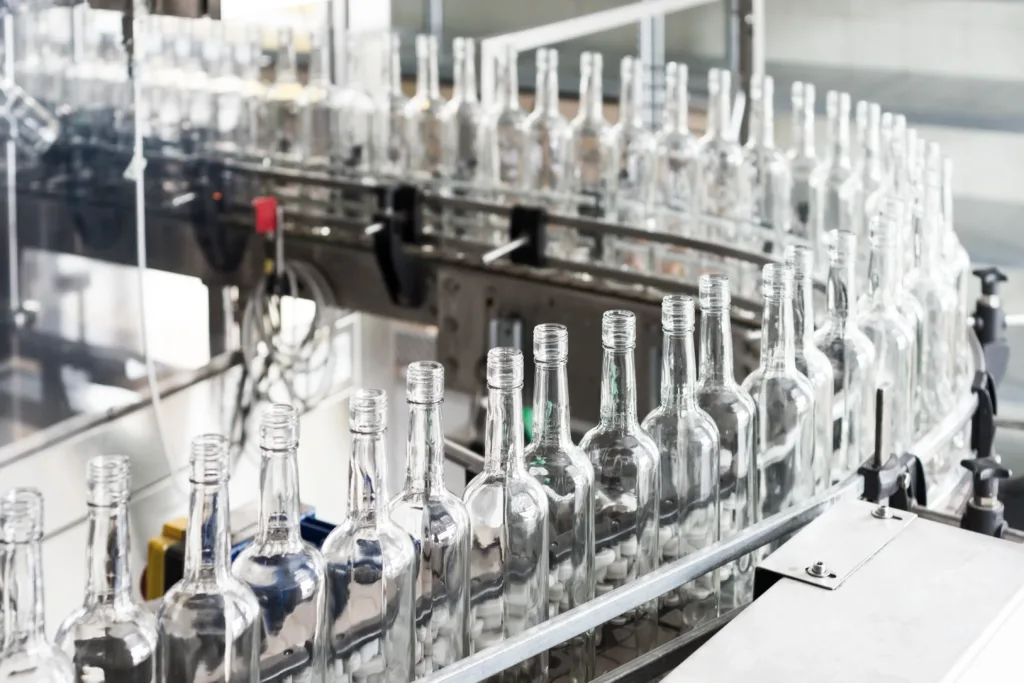
2.Common Challenges in Glass Bottle Manufacturing
Glass Defects and Imperfections
One of the most prevalent challenges in glass bottle manufacturing is the occurrence of defects. Some of the most common defects include:
- Blisters: Small air bubbles trapped in the glass, which can weaken the structure.
- Stones: Foreign particles or unmelted material that can create hard spots in the glass.
- Cords: Strands or streaks caused by uneven melting, leading to weaker sections.
- Cracks: Often formed during cooling or handling, cracks can compromise the bottle’s integrity.
These defects can render the bottle unsuitable for use, especially in industries like pharmaceuticals and food and beverage, where product safety is paramount.
Inconsistent Wall Thickness and Bottle Strength
Another frequent issue is the inconsistent thickness of bottle walls, which can result in weak spots that are prone to breakage. This problem arises due to improper distribution of molten glass during the forming process. Manufacturers must carefully control the flow and temperature of the glass to ensure even distribution and avoid weak or heavy areas.
Temperature Control Issues in the Furnace
Temperature fluctuations in the furnace can cause a host of problems, from inconsistent melting to defects in the glass composition. Maintaining a constant temperature is crucial to ensure that the glass batch is melted uniformly, as even slight variations can lead to color discrepancies or structural weaknesses in the final product.
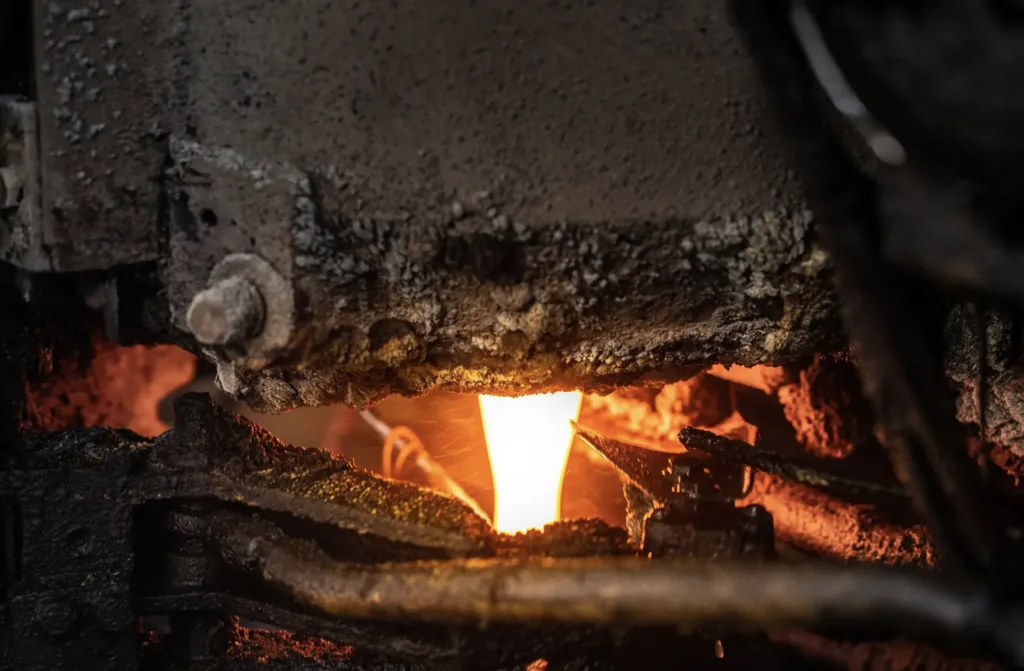
3.Process-Specific Challenges
Mold-Related Problems
Molds play a critical role in shaping glass bottles, and any issues with the molds can lead to defective products. Common mold-related problems include:
- Wear and tear: Over time, molds can become worn, leading to imperfections in the bottle’s shape.
- Misalignment: Misaligned molds can cause visible seams, which not only affect the bottle’s appearance but may also weaken the structure.
Regular mold maintenance and precise alignment are essential to preventing these issues.
Annealing Process Difficulties
The annealing process involves gradually cooling the glass to relieve internal stresses. If this process is not done correctly, the glass may develop residual stresses, making it more likely to crack during filling or transportation. Proper control of the annealing temperature and time is vital to ensure that the glass bottles are strong and durable.
Surface Treatment and Durability Challenges
Glass bottles are often coated with substances like tin oxide or polyethylene to improve surface durability and reduce the risk of scratching. However, problems during surface treatment can result in uneven coatings, which compromise the bottle’s resistance to abrasions and weaken its overall structure.
4.Environmental and Sustainability Challenges
High Energy Consumption
Glass manufacturing is an energy-intensive process, with the furnace consuming the majority of the energy. Melting glass requires significant amounts of fuel, leading to high operational costs and environmental concerns. Reducing energy consumption is a major challenge for manufacturers, who must balance production efficiency with sustainability goals.
Process Stage | Energy Consumption (%) |
---|---|
Melting Furnace | 70-80% |
Forming Machines | 10-15% |
Annealing and Cooling | 5-10% |
Packaging and Handling | 2-5% |
Waste and Material Loss During Manufacturing
The production of glass bottles can generate significant waste, particularly if defective bottles need to be discarded. In addition, cullet (waste glass) from broken or unused bottles must be recycled back into the production process. While recycling cullet reduces the need for raw materials, managing this waste stream efficiently remains a challenge.
5.Quality Control Issues in Glass Bottle Manufacturing
Ensuring Dimensional Accuracy and Consistency
Ensuring that each bottle meets strict dimensional standards is crucial for industries like pharmaceuticals and food and beverage. Bottles must not only look good but also function properly, with consistent size, shape, and wall thickness. Automated inspection systems are commonly used to check for these factors, but even with automation, achieving perfect consistency across large production runs is difficult.
Pressure Resistance and Testing
Many glass bottles, particularly those used for carbonated beverages, must withstand significant internal pressure. Testing for pressure resistance is a critical step to ensure that bottles do not fail during transportation or while in use. Failures in pressure testing are often due to inconsistent wall thickness or defects in the glass.
6.Addressing the Challenges
Innovations and Solutions
- Advanced inspection technologies: Automated systems equipped with cameras and sensors can detect even the smallest defects, helping manufacturers reduce waste and improve quality.
- Energy-efficient furnaces: New furnace designs that use less energy or alternative fuels are being developed to reduce the environmental impact of glass production.
- Improved materials and coatings: Research is ongoing into stronger, lighter materials for glass bottles, as well as more durable surface treatments to increase bottle lifespan.
Future Trends in Glass Bottle Manufacturing
As the industry continues to evolve, several trends are likely to shape the future of glass bottle manufacturing:
- Sustainability: With growing environmental concerns, manufacturers are investing in eco-friendly production methods, such as increasing the use of cullet and developing more energy-efficient processes.
- Smart manufacturing: The use of AI and machine learning in manufacturing is set to improve quality control and reduce downtime by predicting issues before they arise.
- Lightweight glass bottles: Research into lightweight glass aims to reduce material use without compromising strength, helping to cut both production costs and environmental impact.
Conclusion
The challenges in glass bottle manufacturing are numerous and diverse, ranging from technical issues like defects and temperature control to environmental concerns like energy consumption and waste. However, through the adoption of new technologies, improved processes, and a commitment to sustainability, manufacturers are finding ways to overcome these challenges. By addressing these issues head-on, the industry can continue to produce high-quality glass bottles while reducing its environmental footprint and meeting the demands of an ever-evolving market.