In the world of glass bottle manufacturing, quality control is more than just a buzzword—it’s a crucial element that ensures the production of reliable, durable, and consistent products. Whether you’re producing bottles for beverages, pharmaceuticals, or cosmetics, maintaining high standards is essential for both brand reputation and customer satisfaction. This blog post delves into the importance of quality control in glass bottle manufacturing, exploring the processes, technologies, and best practices that manufacturers use to guarantee that every bottle meets the stringent requirements of the industry.
Quality control in glass bottle manufacturing is not only about preventing defects but also about optimizing the entire production process to ensure that the final products are both functional and aesthetically pleasing. By implementing effective quality control measures, manufacturers can minimize waste, reduce costs, and maintain a competitive edge in the market.
This comprehensive guide will cover every aspect of quality control, from the inspection of raw materials to the latest advancements in technology, providing you with an in-depth understanding of how consistency and durability are achieved in glass bottle manufacturing.
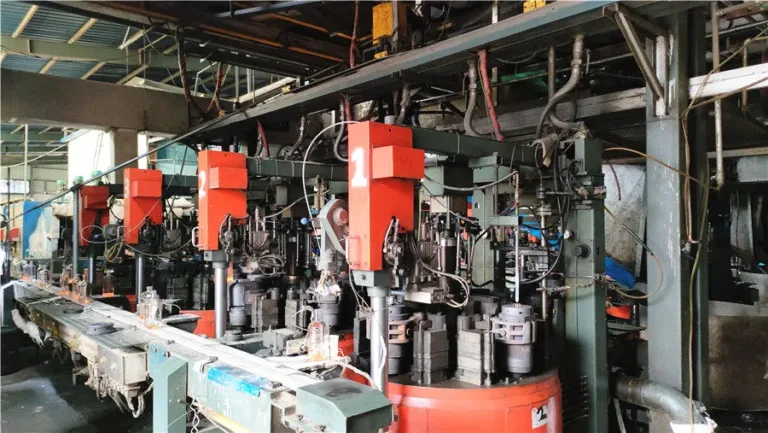
Table of Contents
1.Understanding Quality Control in Glass Bottle Manufacturing
Quality control is the backbone of glass bottle manufacturing, ensuring that each bottle produced meets the required standards of consistency and durability. In this section, we’ll explore the fundamentals of quality control within the industry, focusing on what it entails and why it is essential for successful manufacturing.
What is Quality Control in Glass Bottle Manufacturing?
Quality control in glass bottle manufacturing refers to a set of processes designed to monitor and manage the production of glass bottles to ensure they meet predetermined specifications. This involves systematic inspections, tests, and procedures at various stages of the manufacturing process. The goal is to detect and correct any defects or variations that could compromise the quality, durability, or safety of the final product.
Quality control encompasses everything from the selection of raw materials to the inspection of finished bottles. It involves rigorous checks for factors such as:
- Dimensional accuracy: Ensuring that the bottle meets precise measurements for capacity, neck finish, and overall shape.
- Surface quality: Checking for defects like bubbles, cracks, or scratches that could weaken the bottle or affect its appearance.
- Strength and durability: Testing the bottle’s resistance to impact, pressure, and temperature variations.
By maintaining stringent quality control measures, manufacturers can produce glass bottles that not only look good but also perform reliably in their intended applications. This is particularly important in industries where the integrity of the bottle directly affects the safety and satisfaction of the end consumer, such as in the food and beverage, pharmaceutical, and cosmetic sectors.
Why is Quality Control Essential in Glass Bottle Manufacturing?
The importance of quality control in glass bottle manufacturing cannot be overstated. It serves as a critical component in ensuring that every bottle produced meets the industry’s high standards for safety, durability, and aesthetic appeal. Here are some key reasons why quality control is essential:
Preventing Defects and Failures
Quality control helps identify and eliminate defects early in the production process, reducing the risk of failures that could lead to costly recalls or customer complaints. For example, a bottle with a weak spot or crack could shatter during transportation or use, posing a safety hazard and damaging the brand’s reputation.Ensuring Consistency
In manufacturing, consistency is key. Quality control ensures that each bottle produced is identical in size, shape, and strength, meeting the exact specifications required by the customer. This is particularly important for brands that rely on uniform packaging for branding and product recognition.Cost Efficiency
Implementing effective quality control measures can save manufacturers money by reducing waste, rework, and returns. By catching defects early, manufacturers can address issues before they result in large-scale production errors, thus lowering production costs and increasing profitability.Compliance with Standards and Regulations
The glass bottle manufacturing industry is subject to various standards and regulations, depending on the market and the product’s intended use. Quality control helps ensure compliance with these standards, which is essential for legal and safety reasons. For example, bottles used for pharmaceuticals must meet strict requirements to prevent contamination and ensure the safety of the contents.Enhancing Customer Satisfaction
High-quality bottles that meet or exceed customer expectations can lead to increased customer satisfaction and loyalty. Quality control plays a crucial role in achieving this by ensuring that every bottle delivered to the customer is free from defects and fit for purpose.Protecting Brand Reputation
In today’s competitive market, a brand’s reputation is everything. A single batch of defective bottles can lead to negative reviews, lost customers, and long-term damage to the brand’s image. Quality control helps safeguard the brand by ensuring that only the best products reach the market.
2.Key Quality Control Processes in Glass Bottle Manufacturing
Quality control in glass bottle manufacturing is a multi-faceted process that involves several critical stages, each designed to ensure that the final product meets high standards of consistency and durability. These processes begin with the inspection of raw materials and continue through to the final inspection and testing of the finished bottles. In this section, we will explore the key quality control processes that are essential in glass bottle manufacturing.
Raw Material Inspection
The foundation of high-quality glass bottles starts with the inspection of raw materials. The primary ingredients used in glass manufacturing include silica (sand), soda ash, limestone, and cullet (recycled glass). Each of these materials must be carefully inspected and tested before they enter the manufacturing process to ensure they meet the necessary purity and composition standards.
Key aspects of raw material inspection include:
- Purity Testing: Ensuring that the raw materials are free from contaminants that could affect the clarity, color, or strength of the glass.
- Chemical Composition Analysis: Verifying that the raw materials have the correct chemical composition, which is crucial for achieving the desired properties in the final glass product.
- Moisture Content: Checking the moisture content in the raw materials, as excess moisture can lead to defects such as bubbles or cracks during the glass-forming process.
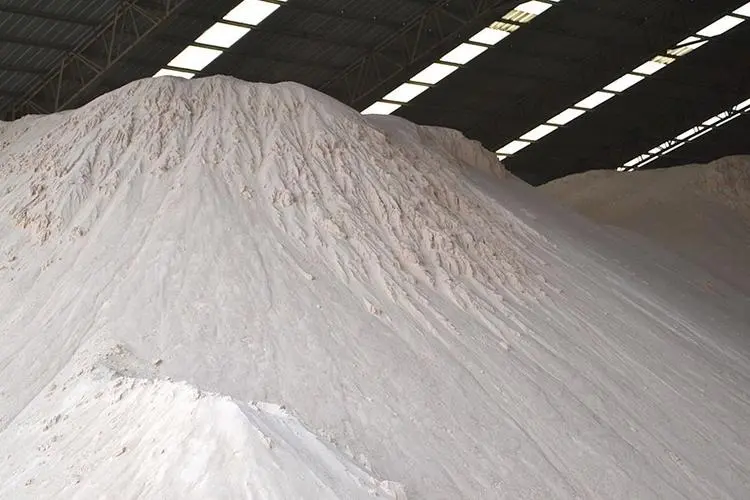
Glass Melting and Forming
The melting and forming process is where raw materials are transformed into molten glass and then shaped into bottles. This stage is critical for ensuring that the glass has the desired properties, such as strength, clarity, and durability.
Key quality control steps in the glass melting and forming process include:
- Temperature Control: Maintaining precise temperature control in the furnace is essential for achieving a uniform melt. Inconsistent temperatures can lead to variations in the glass composition, resulting in defects such as bubbles or weak spots.
- Homogenization: Ensuring that the molten glass is thoroughly mixed to eliminate any variations in composition. This process is crucial for producing bottles with consistent quality.
- Forming Precision: The glass is shaped into bottles using molds, and precision is key. Quality control measures ensure that the molds are accurately maintained and that the forming process produces bottles with the correct dimensions and thickness.
Fact:
Maintaining a consistent furnace temperature, typically between 1,400°C and 1,600°C, is crucial for achieving the desired glass properties. Even slight fluctuations can result in defects that compromise the bottle’s quality.
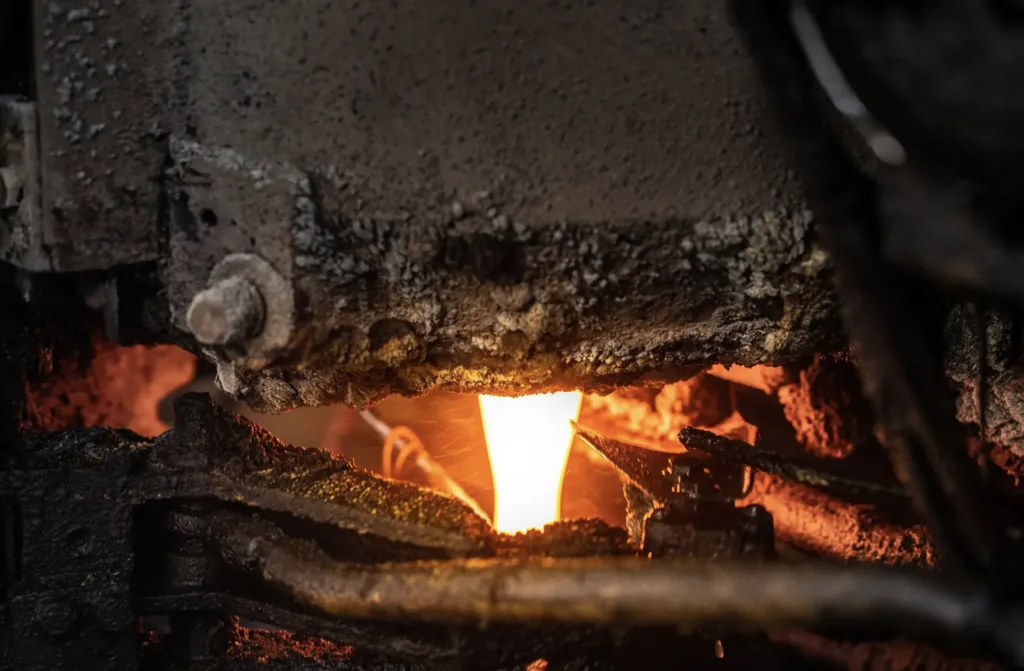
Mold Design and Maintenance
Mold design and maintenance play a pivotal role in the quality of the finished glass bottles. The mold determines the bottle’s shape, size, and surface finish, making it a critical component in the manufacturing process.
Key considerations for mold design and maintenance include:
- Precision Engineering: Molds must be engineered with extreme precision to ensure that the bottles have the correct dimensions and a smooth surface finish.
- Regular Maintenance: Molds are subject to wear and tear over time, which can lead to defects such as seam lines or variations in thickness. Regular maintenance and inspection are essential to ensure that molds remain in optimal condition.
- Cooling Efficiency: Proper cooling of the mold is crucial for preventing defects such as stress cracks or warping. Quality control measures ensure that the cooling process is consistent and effective.
List: Common Mold-Related Defects and Their Causes
- Seam Lines: Caused by misaligned mold parts or worn-out molds.
- Variations in Thickness: Result from uneven cooling or poor mold design.
- Surface Imperfections: Caused by damaged or poorly maintained molds.
Case Study:
A glass bottle manufacturer faced challenges with seam lines appearing on their bottles, leading to increased rejection rates. By implementing a more rigorous mold maintenance schedule and investing in precision-engineered molds, they were able to reduce seam line defects by 30%, resulting in significant cost savings and improved product quality.
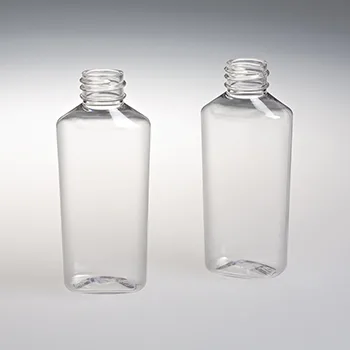
Annealing Process
The annealing process is a crucial step in ensuring the durability and strength of glass bottles. After the bottles are formed, they are gradually cooled in a controlled environment to relieve internal stresses that could cause them to crack or break.
Key aspects of the annealing process include:
- Controlled Cooling: The bottles are passed through an annealing lehr, where they are slowly cooled to prevent the formation of stress points. The cooling rate must be carefully controlled to ensure that the bottles are free from internal tensions.
- Temperature Monitoring: Continuous monitoring of the temperature within the annealing lehr is essential to ensure that the bottles are cooled evenly and consistently.
- Stress Testing: After annealing, bottles are often subjected to stress tests to confirm that they have the necessary strength and are free from defects.
Fact:
The annealing process typically involves cooling the bottles over several hours, with temperatures gradually reduced from around 600°C to room temperature. This slow cooling helps to avoid thermal shock and ensures that the bottles are robust and durable.
Inspection and Testing of Finished Products
The final stage in the quality control process is the inspection and testing of the finished glass bottles. This step ensures that each bottle meets the required specifications and is free from defects before it is shipped to the customer.
Key quality control measures for finished products include:
- Visual Inspection: Each bottle is inspected for visible defects such as bubbles, cracks, or surface imperfections. This can be done manually or with the help of automated systems.
- Dimensional Testing: The bottles are measured to ensure that they meet the specified dimensions for height, diameter, and capacity.
- Strength Testing: Bottles are subjected to tests such as impact resistance, pressure resistance, and thermal shock testing to confirm their durability.
- Leak Testing: For bottles intended to hold liquids, leak testing is performed to ensure that the bottles are airtight and will not leak during use.
3.Common Defects in Glass Bottle Manufacturing and How to Address Them
In the glass bottle manufacturing process, despite the best quality control measures, defects can still occur. Understanding these defects and how to address them is crucial for maintaining high standards of quality and ensuring customer satisfaction. This section will explore some of the most common defects in glass bottle manufacturing, their causes, and effective strategies for addressing them.
1. Surface Defects
Surface defects are among the most visible and common issues in glass bottle manufacturing. These defects can affect the aesthetic appeal of the bottles and may also compromise their structural integrity.
Types of Surface Defects:
- Bubbles (or Blisters): Small air pockets trapped within the glass during the melting or forming process.
- Scratches and Scuffs: Surface abrasions caused by improper handling or equipment malfunction.
- Cracks and Chips: Structural breaks that occur due to thermal shock, improper cooling, or mechanical stress.
Causes:
- Bubbles can form due to improper melting of raw materials or trapped gases during the forming process.
- Scratches are often caused by contact with rough surfaces during transportation or mishandling during the manufacturing process.
- Cracks and chips typically result from thermal stress during rapid cooling or from mechanical impact during handling.
How to Address Surface Defects:
- Improved Melting and Forming: To minimize bubbles, ensure the raw materials are properly mixed and melted at the correct temperatures. Adjusting the forming process to reduce trapped gases can also help.
- Proper Handling: Implementing stricter handling protocols and using protective coatings can reduce the occurrence of scratches and scuffs.
- Controlled Cooling: Enhancing the annealing process by ensuring a gradual and even cooling rate can help prevent cracks and chips.
Case Study:
A glass bottle manufacturer noticed an increase in surface defects, particularly bubbles and cracks. By fine-tuning their melting process and investing in better furnace technology, they reduced the occurrence of bubbles by 40%. Additionally, by improving the annealing process, they were able to reduce cracks and chips by 30%, leading to higher product quality and fewer returns.
2. Dimensional Defects
Dimensional defects refer to variations in the size, shape, or thickness of the glass bottles. These defects can lead to issues with fit, function, and aesthetics, and may cause problems during filling, labeling, or capping.
Types of Dimensional Defects:
- Out-of-Tolerance Dimensions: Bottles that do not meet specified size requirements, such as height, diameter, or neck finish.
- Uneven Thickness: Variations in wall thickness that can lead to weak spots or uneven cooling.
- Misaligned Necks: Necks that are off-center or tilted, leading to problems with capping and sealing.
Causes:
- Mold Wear: Over time, molds can wear down, leading to out-of-specification bottles.
- Improper Forming: Variations in the forming process, such as uneven glass distribution, can result in dimensional defects.
- Cooling Variations: Uneven cooling during the annealing process can cause warping or changes in dimensions.
How to Address Dimensional Defects:
- Regular Mold Maintenance: Implementing a rigorous mold maintenance and replacement schedule can help prevent dimensional variations caused by worn molds.
- Precision Forming: Ensuring that the forming process is precisely controlled, with consistent glass distribution, can reduce the risk of dimensional defects.
- Enhanced Cooling: Improving the uniformity of the cooling process, particularly during annealing, can help maintain consistent dimensions.
Fact:
Dimensional defects can lead to significant issues in automated production lines, where even slight variations can cause jamming, mislabeling, or sealing problems, leading to costly production delays and increased waste.
3. Internal Defects
Internal defects in glass bottles are flaws that occur within the glass itself, often invisible to the naked eye but detrimental to the bottle’s structural integrity. These defects can lead to unexpected breakage, especially under pressure or during transportation.
Types of Internal Defects:
- Stones: Solid impurities embedded within the glass, often originating from raw materials.
- Inclusions: Foreign particles trapped inside the glass during the melting process.
- Striae (or Cords): Streaks or lines within the glass caused by uneven mixing or temperature variations during melting.
Causes:
- Contaminated Raw Materials: Impurities in the raw materials can lead to stones and inclusions.
- Inconsistent Melting: Variations in furnace temperature or insufficient mixing can cause striae and other internal defects.
- Equipment Wear: Worn or damaged furnace components can introduce contaminants or create uneven temperatures, leading to internal flaws.
How to Address Internal Defects:
- Raw Material Quality Control: Implementing stricter controls on the quality of raw materials, including thorough inspection and testing, can reduce the occurrence of stones and inclusions.
- Furnace Maintenance and Monitoring: Regular maintenance of the furnace and continuous monitoring of temperature and mixing conditions can help prevent striae and other internal defects.
- Advanced Inspection Techniques: Using non-destructive testing methods, such as ultrasonic or optical scanning, can help detect internal defects before the bottles are shipped.
4. Thermal Shock Resistance Issues
Thermal shock resistance refers to a glass bottle’s ability to withstand sudden changes in temperature without cracking or breaking. Bottles with poor thermal shock resistance are prone to breakage when exposed to rapid temperature fluctuations, such as during filling with hot liquids or exposure to cold environments.
Causes:
- Inconsistent Annealing: Improper or uneven annealing can leave residual stresses in the glass, making it more susceptible to thermal shock.
- Variations in Glass Composition: Differences in the chemical composition of the glass can affect its thermal properties, leading to varying resistance to temperature changes.
- Uneven Thickness: Bottles with uneven wall thickness are more likely to experience thermal stress and break under sudden temperature changes.
How to Address Thermal Shock Resistance Issues:
- Enhanced Annealing Process: Ensuring a uniform and carefully controlled annealing process can significantly improve thermal shock resistance by relieving internal stresses.
- Consistent Glass Composition: Maintaining strict control over the glass composition during manufacturing can help ensure consistent thermal properties across all bottles.
- Design Considerations: Designing bottles with uniform wall thickness and avoiding sharp angles or edges can reduce the risk of thermal shock.
Fact:
Thermal shock resistance is especially critical for bottles used in the food and beverage industry, where sudden temperature changes are common during processing and consumption.
5. Color Variations
Color variations in glass bottles can be a significant quality concern, particularly for brands that rely on specific colors for brand identity. Even slight variations in color can result in rejected batches and increased production costs.
Causes:
- Inconsistent Raw Materials: Variations in the quality or composition of raw materials, particularly cullet, can lead to differences in the final color of the glass.
- Improper Melting Process: Temperature fluctuations during the melting process can affect the way colorants interact with the glass, leading to inconsistent coloring.
- Contamination: Foreign materials or impurities introduced during manufacturing can alter the intended color of the glass.
How to Address Color Variations:
- Strict Raw Material Control: Ensuring that raw materials, especially colorants, are consistent in quality and composition can help maintain uniform color across all batches.
- Stable Melting Conditions: Maintaining consistent furnace temperatures and carefully controlling the melting process can reduce the risk of color variations.
- Regular Testing and Monitoring: Conducting regular colorimetric testing and visual inspections throughout the manufacturing process can help identify and address color variations early.
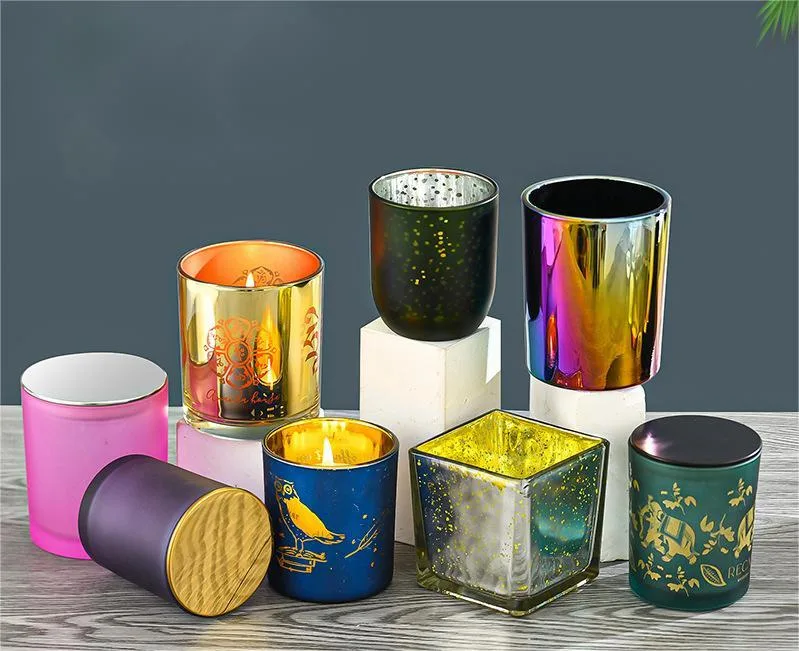
Conclusion
Quality control in glass bottle manufacturing is essential for ensuring that products meet high standards of consistency, durability, and safety. By defining quality standards, utilizing advanced inspection technologies, implementing effective CAPA processes, and adhering to industry regulations, manufacturers can achieve superior quality outcomes. Engaging employees in quality control efforts and managing supplier quality are also crucial for maintaining high standards and driving continuous improvement.